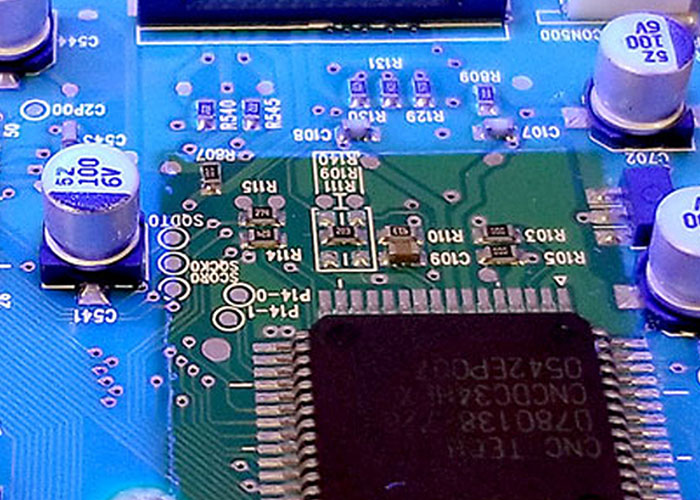
Conformal Coatings
MG Chemicals hat ein umfassendes Angebot an Schutzbeschichtungen (Conformal Coatings) entwickelt, die speziell darauf ausgelegt sind, den modernen Anforderungen für den Schutz von Leiterplatten und Baugruppen zu entsprechen. Diese innovativen Produkte schützen elektronische Schaltungen vor üblichen Einflüssen wie Feuchtigkeit, Staub und Chemikalien, was die Lebensdauer der Elektronik deutlich verlängert.
Die Produktlinie bietet Acryl, Polyurethan, Epoxidharz, Silikon und UV-härtende Materialien. Diese Auswahl ermöglicht es den Anwendern, eine auf ihre spezifischen Schutz- und Verarbeitungsanforderungen zugeschnittene Lösung zu finden.
Die Produkte sind in verschiedenen Viskositäten verfügbar, was sie ideal für das Auftragen per Pinsel oder selektives Sprühen macht. Zudem erfüllen sie die hohen Industriestandards, wie sie in den Normen IPC-CC-830C und UL746E festgelegt sind. Nehmen Sie gerne direkt Kontakt mit uns auf, um die für Ihre Anwendung beste Schutzbeschichtung zu finden.
Was sind Schutzbeschichtungen?
Schutzlacke sind klare, flexible Decklacke, die sich an die komplizierten Geometrien von Leiterplatten anpassen. Sie werden auf Leiterplatten aufgebracht, um diese robuster zu machen und dadurch die Produktlebensdauer zu verlängern.
Arten von Schutzbeschichtungsmaterialien
Derzeit gibt es acht verschiedene Familien von Schutzbeschichtungen, wie im IPC-CC-830C-Standard festgelegt . Dazu gehören Acryl-, Polyurethan-, Silikon-, Epoxid-, UV-härtbare, Parylen-, ultradünne und Styrol- Blockcopolymertypen. Die folgende Tabelle fasst die Vor- und Nachteile der einzelnen Beschichtungsarten zusammen.
Material | Vorteile | Nachteile |
Acryl | Benutzerfreundlichkeit, niedrige Kosten | Schlechte Lösungsmittelbeständigkeit |
Polyurethan | Abriebfestigkeit | Lange Aushärtezeiten |
Epoxidharz | Chemikalien- und Kratzfestigkeit | Schwierig zu verwenden und nachzuarbeiten |
Silikon | Hohe Temperaturbeständigkeit | Schlechte Lösungsmittelbeständigkeit |
UV-Härtung | Sehr schnelle Aushärtezeit | Teuer, hohe Kapitalkosten |
Parylene | Völlig konform und einheitlich | Teuer, schwierig anzuwenden |
Ultra dünn | Schnelle Aushärtung, gute Hydrophobie | Weniger Oberflächenschutz als andere Beschichtungen |
Styrol- Blockcopolymer | Überragender Feuchtigkeitsschutz | Schlechte Lösungsmittelbeständigkeit |
Die Wahl der richtigen Technologie hängt hauptsächlich von folgenden Überlegungen ab: Welche Zertifizierungen (falls vorhanden) wird benötigt? Was sind die größten Umweltprobleme, vor denen geschützt werden muss? Und welche Verarbeitungsmöglichkeiten sind möglich? Letztendlich kommt es bei der richtigen Materialauswahl darauf an, alle Ihre Anforderungen zu kennen. Bitte wenden Sie sich an unseren technischen Support, wenn Sie Hilfe benötigen.
Acryl-Schutzbeschichtungen
1-Komponenten-Acryl-Schutzbeschichtungen werden aufgrund ihrer einfachen Anwendung, einfachen Reparatur und hervorragenden Feuchtigkeitsbeständigkeit am häufigsten verwendet.
Erhältlich sowohl in flüssiger als auch in Aerosolform.
Polyurethan-Schutzbeschichtungen
1-Komponenten-Beschichtungen, die für ihre Vielseitigkeit, Flexibilität, Haftung und Kratzfestigkeit bekannt sind. Polyurethan-Schutzbeschichtungen finden Anwendung in raueren Umgebungen, insbesondere dort, wo korrosive Einflüsse vorhanden sind.
Erhältlich sowohl in flüssiger als auch in Aerosolform.
Silikon-Schutzbeschichtungen
Silikonbeschichtungen sind sowohl als reines Silikon als auch als Silikon/Acryl-Hybridsystem erhältlich und bieten im Vergleich zu anderen Chemikalien einen verbesserten Wärmeschutz und einen breiteren Betriebstemperaturbereich.
Erhältlich sowohl in flüssiger als auch in Aerosolform.
Epoxid- Schutzbeschichtungen
Epoxid- Schutzbeschichtungen sind ideale Materialien für Leiterplatten, die den härtesten Bedingungen ausgesetzt sind. Erwägen Sie die Verwendung einer Epoxidbeschichtung, wenn Ihre Platine korrosiven Elementen, chemischen Lösungsmitteln oder Schäden durch starke Partikel ausgesetzt ist.
Nur in flüssiger Form erhältlich.
UV-härtende Schutzbeschichtungen
Bei hohen Verarbeitungsanforderungen ermöglichen UV-härtende Schutzbeschichtungen eine schnelle Taktzeit ohne Qualitätseinbußen.
Nur in flüssiger Form erhältlich.
Isolierbeschichtungen
Isolierbeschichtungen unterscheiden sich von Schutzbeschichtungen aufgrund ihrer verbesserten Isoliereigenschaften und bieten eine praktische Lösung, wenn die elektrische Isolierung von Hochspannungsteilen wie Motorwicklungen und Spulen erforderlich ist.
Schutzbeschichtungssprays
Aerosole sind für Acryl-, Polyurethan- und Silikon/Acryl-Hybridprodukte erhältlich und bieten die Vorteile des Sprühauftrags, ohne dass teure pneumatische Geräte installiert werden müssen, was sie ideal für Projekte mit geringem Volumen macht.
Abbeizmittel für Schutzbeschichtungen
Eine leistungsstarke Kombination von Lösungsmitteln, die chemische Bindungen auflöst und es Ihnen ermöglicht, unerwünschte Beschichtungen oder Klebstoffe zu entfernen. Für eine selektivere Entfernung ist es auch als Gel erhältlich.
Verdünner
Lösungsmittel zum Verdünnen von Schutzbeschichtungen für eine bessere Anwendung. Empfohlene Verdünner finden Sie im technischen Datenblatt der Schutzbeschichtung.
Isolier- und Schutzstifte
Sie eignen sich perfekt für punktuelle Reparaturen auf Leiterplatten und enthalten eine 419D- Acryl-Schutzbeschichtung, erhältlich in mehreren Farben für kleinere Ausbesserungen.
Wie werden Schutzbeschichtungen verwendet?
Schutzbeschichtungen werden verwendet, um die Lebensdauer von Leiterplatten zu verlängern, indem sie eine Schutzschicht gegen häufige Umwelteinflüsse wie Feuchtigkeit, Staub, Schmutz und Pilze bilden. Diese Beschichtungen verfügen über hervorragende dielektrische Eigenschaften, die dazu beitragen, einen Überschlag zu verhindern , wodurch Leiterbahnen näher beieinander platziert werden können und dadurch die Entwicklung kleinerer, leistungsstärkerer Elektronikkomponenten erleichtert wird.
Schutzbeschichtungsstandards
Es gibt zwei Hauptstandards für Schutzlacke: UL746E und IPC-CC-830. Der UL746E Conformal Coating Standard umfasst eine Reihe dielektrischer Tests, die die Isolationseigenschaften der Beschichtung nach Umwelteinflüssen sowie ihre Flammhemmung messen. Der IPC-CC-830-Standard wurde vom Institute for Printed Circuits (IPC) erstellt , um den MIL-I-46058C-Standard zu ersetzen, der 1998 für inaktiv erklärt wurde. Dieser Standard testet die Haltbarkeit der Beschichtung gegenüber Thermoschock, hydrolytischer Alterung und Feuchtigkeitssättigung , Pilzresistenz und Flammschutz.
In diesen beiden Artikeln haben wir detailliertere Informationen zu den Standards UL746E und IPC-CC-830 bereitgestellt.
Den IPC-CC-830-Standard verstehen
Den UL 746E-Standard verstehen
Mängel und Probleme bei der Schutzbeschichtung
Bei Schutzlacken treten dieselben Mängel auf wie beim Auftragen von Lacken. Indem Sie lernen, wie man eine Schutzbeschichtung aufträgt, können Sie die Bearbeitungszeit optimieren und Probleme an der Lackierstraße vermeiden. Nachfolgend finden Sie eine Zusammenfassung der häufigsten Beschichtungsfehler und wie diese behoben werden können.
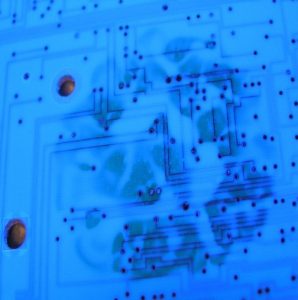
Benetzung
Entnetzung tritt auf, wenn sich eine Beschichtung nicht über Teile des Substrats ausbreitet (oder benetzt) und anschließend angrenzende Bereiche überschwemmt. Dies geschieht, wenn übliche Rückstände wie Flussmittel, Fett, Öl oder Schneidflüssigkeit auf der Oberfläche verbleiben und den natürlichen Verlauf der Beschichtung behindern sowie deren Ausbreitung und Nivellierung verhindern. Die Lösung besteht darin, den Untergrund gründlich zu reinigen , bis keine Verunreinigungen mehr vorhanden sind.
Orangenschale
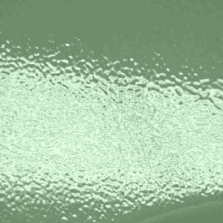
Orangenhaut
Wie der Name schon sagt, führt „Orangenhaut“ zu einer holprigen, konturierten Oberfläche, die einer Orangenschale ähnelt. Dieses Problem ist auf falsch eingestellte Sprühtechnik oder die Verwendung des falschen Verdünners zurückzuführen, was zu einer unzureichenden Zerstäubung führt. Vermeiden Sie „Orangenhaut“, indem Sie die im technischen Datenblatt (TDS) des Produkts empfohlenen Sprüheinstellungen und Verdünner verwenden.
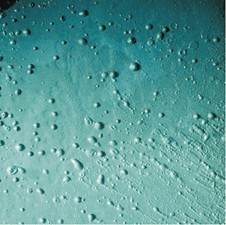
Blasenbildung in der Oberfläche
Dies wird durch drei Dinge verursacht: 1) Auftragen der Beschichtung mit zu hohem Druck, wodurch Luft in die flüssige Beschichtung eindringt. 2) Die Schicht zu schnell trocknen lassen, sodass der Film nicht genügend Zeit hat, sich auszugleichen und zu entlüften. 3) Zu dicker Schichtauftrag wodurch Lösungsmitteldämpfe eingeschlossen werden.
Um „Blasenbildung in der Oberfläche“ zu unterbinden, vermeiden Sie den einmaligen Auftrag dicker Schichten; Bauen Sie stattdessen die notwendige Filmdicke durch mehrmaliges auftragen von dünnen Schichten auf. Die empfohlenen Sprüheinstellungen und die Trocknungszeit für jedes Produkt finden Sie in den technischen Datenblättern von MG Chemicals.
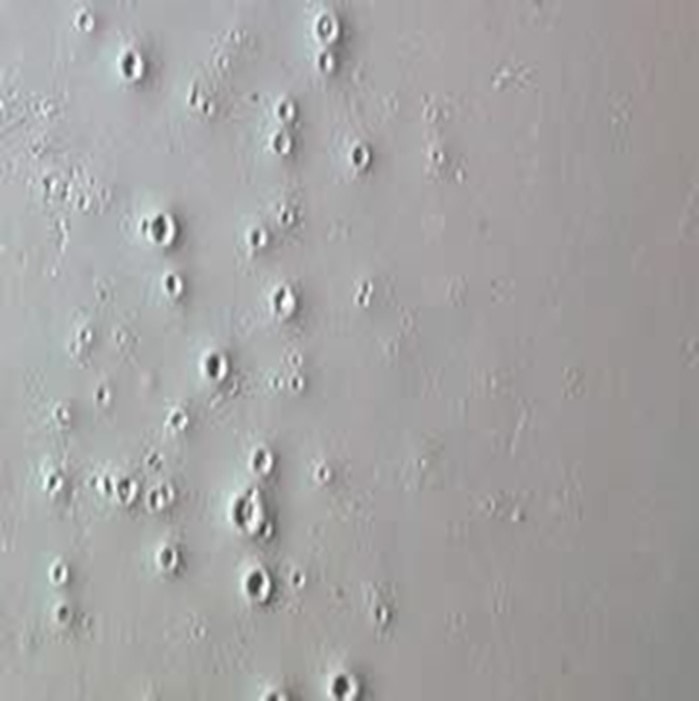
Fischaugen
Fischaugen sehen aus wie kleine kreisförmige Klumpen mit Grübchen in der Mitte. Sie werden normalerweise durch Verunreinigungen durch Öl und Schmutz in den Leitungen der Sprühausrüstung verursacht. Um dieses Problem zu lösen, installieren Sie einfach einen Filter, der sicherstellt, dass zum Sprühen der Beschichtung nur saubere Luft verwendet wird.
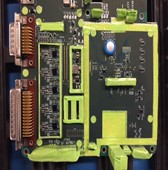
Overspray
Overspray bei Schutzlacken entsteht, wenn die Beschichtung versehentlich auf den falschen Bereich aufgetragen wird. Dies kann passieren, wenn die natürliche Beweglichkeit niedrigviskoser Flüssigkeiten dazu führt, dass sie sich in ungeeignete Bereiche ausbreiten (bekannt als „Dochtwirkung“ oder Kapillarwirkung), durch Bedienerfehler oder durch unkontrollierte Benetzung von aerosolisierten Flüssigkeitsbeschichtungen. Die Abhilfe: Versuchen Sie nicht, Overspray zu vermeiden, sondern antizipieren Sie es und ergreifen Sie vorbeugende Maßnahmen – nämlich Maskieren.
Beim Abdecken wird ein Schutzmaterial wie Malerband oder abziehbares Latex an Stellen angebracht, an denen die Beschichtung nicht erwünscht ist. Sobald die Beschichtung aufgetragen wurde, sollte die Abdeckung vor dem Trocknen schnell entfernt werden, um ein unerwünschtes Entfernen der ausgehärteten Beschichtung zu verhindern.
Prozess zur konformen Beschichtung von Leiterplatten
Das Aufbringen einer Schutzbeschichtung erfordert mehrere Folgeprozesse, um sowohl eine ordnungsgemäße Abdeckung als auch ein ästhetisches Finish zu erzielen.
PCB-Reinigung – Um Beschichtungsfehler wie Benetzungsstörungen zu vermeiden und einen glatten, homogenen Film zu erzielen, müssen Substrate gründlich gereinigt werden, um unerwünschte Verunreinigungen wie Flussmittel, Fett und Öl zu entfernen. MG Chemicals verfügt über ein umfangreiches Portfolio an Reinigungsprodukten, um sicherzustellen, dass Oberflächen sauber und für die Schutzbeschichtung bereit sind.
Maskierung – Um ein Übersprühen der Schutzbeschichtung zu verhindern, bei dem sich die Beschichtung in unerwünschten Bereichen ablagert, müssen Substrate in Sperrbereichen abgedeckt werden. Die Maskierung erfolgt entweder durch die Verwendung einfacher Materialien wie Malerband oder einer abziehbaren Lötstoppmaske wie MG's 862. Es ist wichtig, die Maskierung kurz nach dem Auftragen und vor dem Aushärten der Beschichtung zu entfernen, um ein Ablösen der Beschichtung zu vermeiden.
Aufbringen von Schutzbeschichtungen – Abhängig von der Menge der zu beschichtenden Teile und den Fähigkeiten Ihres Unternehmens können verschiedene Beschichtungstechniken eingesetzt werden.
Für kleine Reparaturen und Arbeiten mit geringem Volumen ist der Pinselauftrag eine ideale Technik, da keine Vorbereitung erforderlich ist. Es ist sehr präzise und erfordert keine Fachkenntnisse. Das Eintauchen eignet sich auch ideal für Prozesse mit geringen Stückzahlen, für ein zuverlässiges Eindringen der Beschichtung unter Komponenten und für eine allgemein schnelle Verarbeitung, erfordert jedoch möglicherweise ein intensives Maskieren und kann in der Handhabung schmutzig sein.
Bei großvolumigen Projekten gewinnt die Sprühtechnik an Bedeutung und ist ideal, wenn eine schnelle Durchlaufzeit, eine bessere Kantenabdeckung und eine bessere Gleichmäßigkeit des Films erforderlich sind.
Das Sprühen kann mit einer einfachen pneumatischen Spritzpistole in einer speziellen Abzugskabine erfolgen. Diese Technik erfordert jedoch einige Fachkenntnisse und erfordert möglicherweise eine Maskierung. Der Sprühprozess kann durch den Einsatz automatisierter Geräte der Art von PVA , Nordson Asymtek und Specialty Coating Systems rationalisiert werden. Diese Systeme bieten Geschwindigkeit und Präzision, um den Durchsatz zu maximieren und Nacharbeiten zu minimieren.
Aushärtung – Es gibt drei Arten von Schutzlacken, die nach ihren Aushärtungsmechanismen klassifiziert werden: thermoplastisch, duroplastisch und UV-härtbar. Zu den thermoplastischen Materialien gehören Acryl und Silikon/Acryl-Hybridbeschichtungen. Sie härten durch physikalisches Trocknen aus, da das Lösungsmittel einfach verdunstet und der Beschichtungsfilm zurückbleibt. Diese Beschichtungen können entweder unter Umgebungsbedingungen oder durch Hitze ausgehärtet werden. Duroplaste sind Materialien, die im Rahmen ihres Aushärtungsmechanismus eine chemische Reaktion eingehen. Wie Thermoplaste können sie typischerweise unter Umgebungsbedingungen ausgehärtet werden. Um optimale Eigenschaften und eine vollständige Aushärtung zu erreichen, benötigen diese Beschichtungen jedoch erhöhte Temperaturen. UV-härtbare Materialien sind Acrylate und Methacrylate, die aushärten, wenn sie bestimmten Wellenlängen von UV-Licht ausgesetzt werden.
Qualitätskontrolle – Der Hauptaspekt bei der Prüfung von Schutzbeschichtungen ist die Abdeckung. Mit einer UV-Lampe geht das schnell und einfach. Bei Bestrahlung der Baugruppe mit UV-Licht reflektieren die beschichteten Bereiche blau fluoreszierend.
Messung der Dicke von Schutzbeschichtungen – Typische Trockenfilmdicken von Schutzbeschichtungen liegen zwischen 1 und 5 Mil (25,4 und 127 μm) und können mit den folgenden Techniken überprüft werden:
Mikrometer – Eine einfache zerstörungsfreie Methode besteht darin, Punkte entlang des unbeschichteten Substrats mit kalibrierten Mikrometern zu messen und diese Punkte anschließend erneut zu messen, wobei der Unterschied die Beschichtungsdicke ist.
Positector – Eine weniger umständliche, zerstörungsfreie Technik verwendet ein digitales Schichtdickenmessgerät, das Änderungen in magnetischen oder elektrischen Feldern misst, um die Schichtdicke zu bestimmen. Obwohl diese Technik viel schneller und einfacher ist, ist sie auf den Einsatz auf leitfähigen Substraten beschränkt und kann daher keine Beschichtungsdicken über Lötstopplack oder anderen isolierten Komponenten messen.
Mikroschnittanalyse – Das einfachste zerstörungsfreie Werkzeug zur Messung der Schichtdicke ist ein Nassfilmmessgerät mit einer schwarzen Lampe. Allerdings ist dieses Verfahren nur bei High-Solid-Systemen, wie zum Beispiel UV-Lacken, anwendbar. Für hochpräzise Schichtdickenmessungen kann schließlich eine Querschnittsanalyse angewendet werden, bei der ein Abschnitt des beschichteten Substrats herausgeschnitten und in eine Kunststoffform montiert wird. Anschließend wird der Querschnitt poliert und unter einem leistungsstarken Mikroskop analysiert, um die Beschichtungsdicke an verschiedenen Stellen zu messen. Obwohl diese Technik die genauesten Messungen liefert, erfordert sie viel Zeit und kostspielige Ausrüstung und zerstört die Probe.
Nacharbeit/Reparatur – Gelegentlich sind Reparaturen erforderlich, um Bereiche auszubessern, an denen die Beschichtung beschädigt, delaminiert ist oder auf andere Weise vom Substrat entfernt wurde. Dies geschieht typischerweise auf einer sehr kleinen Fläche, die eine präzise Anwendung erfordert. Daher werden diese Reparaturen typischerweise mit einem Pinsel aufgetragen, um die erneut aufgetragene Beschichtung zu lokalisieren und auf einen kleinen Bereich zu beschränken.
Vergleich der Schutzbeschichtungen
Überlegungen
Die Wahl der richtigen Schutzbeschichtung hängt von Ihren Materialanforderungen ab – nämlich davon, welche Zertifizierungen ( IPC oder UL ?) erforderlich sind, welchen Umgebungsbedingungen die Beschichtung standhalten muss und welche Verarbeitungsmöglichkeiten Sie haben. Deshalb sollten Schutzbeschichtungen nicht nach der Besten-zu-Schlechten-Rangliste bewertet werden, sondern vielmehr nach der besten Eignung. Beispielsweise benötigt eine Platine für den Innenbereich nicht den extremen Schutz, den ein Epoxidharz bietet, sondern lediglich eine einfache konforme Acrylbeschichtung, die vor Staub und elektrischen Überspannungen schützt.
Umgekehrt wird eine Leiterplatte unter der Motorhaube eines Autos verbaut, ist ein verbesserter Schutz durch Epoxid- oder UV-härtende Materialien erforderlich, die Kraftstoffdämpfen, Streusalz und häufigen Stößen standhalten können. Bei der Auswahl eines Beschichtungssystems muss jede Schutzbeschichtungstechnologie sowohl auf ihre Stärken als auch auf ihre Schwächen hin bewertet und gegen Ihre spezifischen Anforderungen abgewogen werden.
Acryl – Acryl ist ein hervorragendes Material für milde Umgebungen, in denen die Gefahr besteht, dass es zeitweise Feuchtigkeit, Salznebel, Staub und Pilzen ausgesetzt ist. Seine Stärken sind niedrige Kosten, Benutzerfreundlichkeit und Nacharbeit. Sein Nachteil ist die geringe chemische Beständigkeit.
Polyurethan – Polyurethane bieten den gleichen Schutz wie Acryl sowie eine gewisse Beständigkeit gegenüber chemischen Lösungsmitteln, zeichnen sich durch eine hervorragende Abriebfestigkeit aus und behalten eine starke Haftung bei niedrigen Temperaturen bei. Ihr Nachteil ist ihre relativ lange Aushärtezeit, wodurch sie für Anwendungen mit hohem Volumen nicht ideal sind.
Epoxidharz – Epoxidharze bieten im Vergleich zu Acryl, Polyurethan und Silikon einen besseren Schutz. Sie schützen vor häufigen Verunreinigungen wie Feuchtigkeit, aber auch vor aggressiven Chemikalien und Abrieb und tragen dazu bei, Lötstellen vor Stößen zu schützen. Die Anwendung kann aufgrund der langen Aushärtungszeit relativ umständlich sein, sodass ihre Verwendung im Allgemeinen auf Anwendungen beschränkt ist, die einen verbesserten Schutz erfordern.
Silikon – Silikone werden vor allem wegen ihrer hohen Temperaturbeständigkeit und Elastizität geschätzt. Im Vergleich zu den meisten anderen Schutzbeschichtungsarten haben Silikone einen außergewöhnlich niedrigen Modul, was sie ideal für die Beschichtung empfindlicher oberflächenmontierter Geräte oder für Anwendungen mit starken Temperaturwechseln macht. Silikonbeschichtungen werden nicht verwendet, wenn ein Schutz vor Ölen und anderen Lösungsmitteln erforderlich ist, und können im Vergleich zu anderen Produkten manchmal unerschwinglich sein.
UV-Härtung – UV-härtende Materialien zeichnen sich durch unübertroffene Härtungsgeschwindigkeiten aus. Die Aushärtung anderer Chemikalien dauert Stunden, UV-Materialien können jedoch in Sekundenschnelle ausgehärtet werden, was zu einem hohen Durchsatz beiträgt und sie ideal für großvolumige Projekte macht. Um ihren vollen Nutzen zu erzielen, sind jedoch erhebliche Investitionen erforderlich, einschließlich automatisierter Sprühgeräte, Radiometer und Aushärtungslampen/Fördersysteme. Bevor Sie sich für UV entscheiden, sollte daher eine gründliche Kosten-Nutzen-Analyse durchgeführt werden.
Parylene – Parylene unterscheidet sich von allen anderen Schutzbeschichtungstechnologien dadurch, dass es sich um ein Pulver handelt, das durch einen Prozess, der als chemische Gasphasenabscheidung bekannt ist, auf Leiterplatten aufgetragen wird . Dieser Prozess ist äußerst umständlich und erfordert hochspezialisierte Ausrüstung. Die ausgehärtete Beschichtung bietet jedoch eine unübertroffene elektrische Isolierung, Gesamtabdeckung und Temperaturbeständigkeit. Parylene kommt ausschließlich dann zum Einsatz, wenn ein völlig homogener Film erforderlich ist.
Abbildung 1: Radardiagramm zum Vergleich von 6 gängigen Schutzbeschichtungstypen
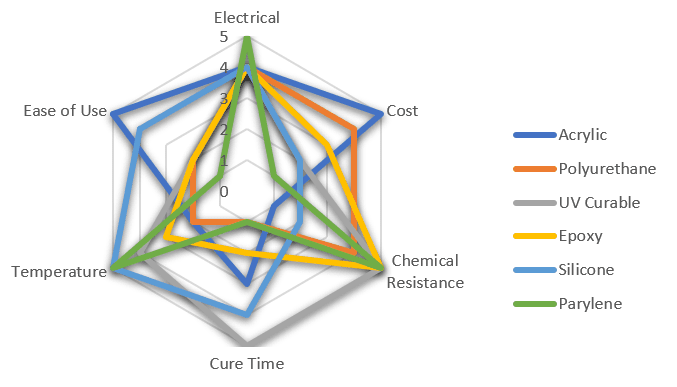